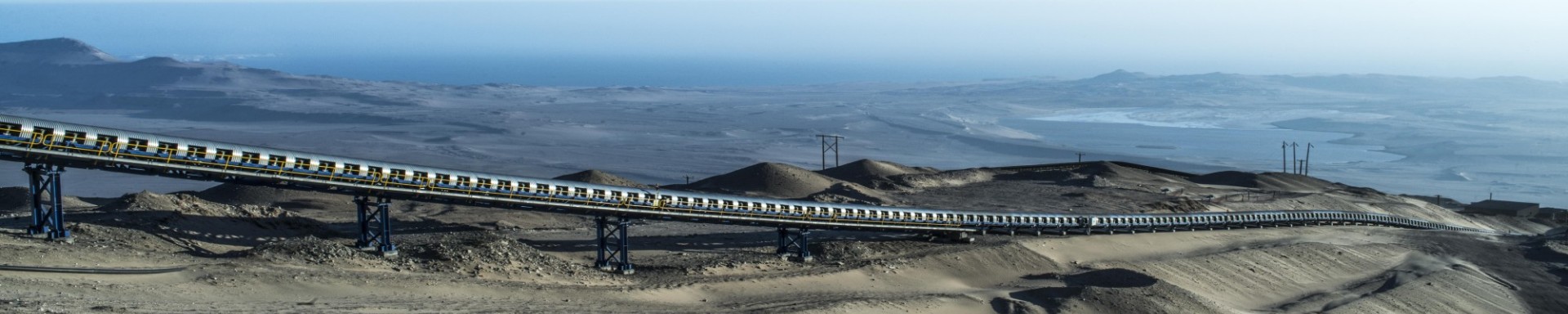
DIAPHRAGM COUPLING INSTALLATION AND TEMPERATURE ADAPTATION
2024-05-16 15:00The diaphragm coupling is very delicate in structure and may cause damage if misused or not installed correctly.Therefore, it is very necessary to ensure that the deviation is within the tolerance range of the normal operation of the disc coupling.
For a straight shaft, place the key into the keyway on the shaft. The end of the key should not protrude or recess into the end of the shaft. It is better to be flush.Place the hub in an oil tank and heat it to a temperature of 120 to 150°C.After heating and insulation, quickly install the diaphragm elastic coupling at the required position on the shaft according to the installation diagram and pay attention to the position marks. The installation plate and the shaft end should generally be flush.Local heating is not allowed during heating to avoid deformation of the disc elastic coupling.For tapered shafts: Install the key on the shaft according to the same requirements as installing keys on a straight shaft, then install the hub on the shaft, push it tightly by hand, and then tighten with nuts to move the hub axially to its fixed position.
Diaphragm couplings can adapt to high temperatures (-80+300) and harsh environments, and can operate under shock and vibration conditions.Elastic disc couplings require no lubrication and routine maintenance;The status of the diaphragm elastic coupling can be detected without disassembly;In addition, during the operation of the equipment, the diaphragm can be inspected using a strobe light.The disc coupling has high torsional stiffness and zero rotation;If the installation and alignment are accurate, the disc elastic coupling will not be damaged throughout its life and has a long life;No wearing parts, can be used in various harsh working conditions;If the offset error is within a limited range, the diaphragm elastic coupling will have the same long life as the equipment;Super torque operation design, the peak torque is twice the rated torque.
It is worth noting that due to the strong rigidity of the elastic disc coupling, if the deviation between the two shafts is too large when the equipment is installed, the diaphragm coupling will produce great axial stress on the thrust bearing on the shaft.Therefore, the guiding and positioning capabilities of the diaphragm group are very critical for the application of diaphragm elastic couplings, especially in high-speed applications.